Blow Molding
Comprehensive Blow Molding Services Backed by Engineering and Manufacturing Excellence
Our blow molding capabilities are built on more than 40 years of hands-on experience, allowing us to deliver scalable, cost-effective container solutions across industries.
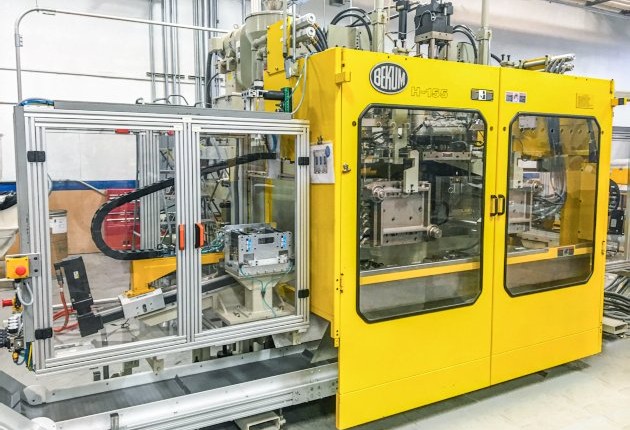
High-Efficiency Blow Molding for Bottles, Containers, and Custom Parts
Lomont Molding offers advanced blow molding capabilities developed through decades of hands-on industry experience. Our fully integrated processes are designed to handle everything from small-run specialty containers to large-volume production of bottles and custom parts.
With a focus on material versatility, consistent quality, and production scalability, we serve industries ranging from pharmaceuticals and personal care to food, beverage, and industrial packaging.
Whether you need lightweight designs, specialized geometries, or high-throughput capacity, our blow molding services are engineered for reliability and precision.
What sets Lomont apart from the competition?
Versatility
We mold small, medium, and multi-part products using continuous, accumulating head, and reciprocating screw configurations. Our equipment supports many standard and specialty polymers, with shot sizes up to 7 pounds and up to 4-cavity designs.
Efficiency
Injection blow molding combines injection molding and blow molding in a single integrated process, reducing production steps and cycle times. The result: faster lead times and greater throughput.
Proved Experience
R&D Molders began molding in 1974, and today their legacy continues under Lomont. With nearly 50 years of experience in blow molding, our team brings industry insight and practical know-how to every project.
Complex Shapes & Finishes
Our process supports unique bottle geometries, multiple neck finishes, and complex design elements such as integrated handles, curves, or logos; ideal for branding and custom packaging.
Key Advantages of Blow Molding
Design Freedom
Supports custom bottle shapes, neck finishes, and branding elements like embossing. Our design and process differentiate your product in the marketplace.
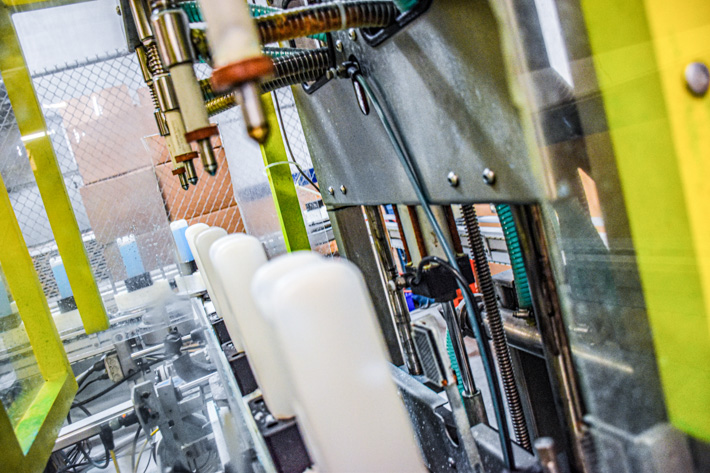
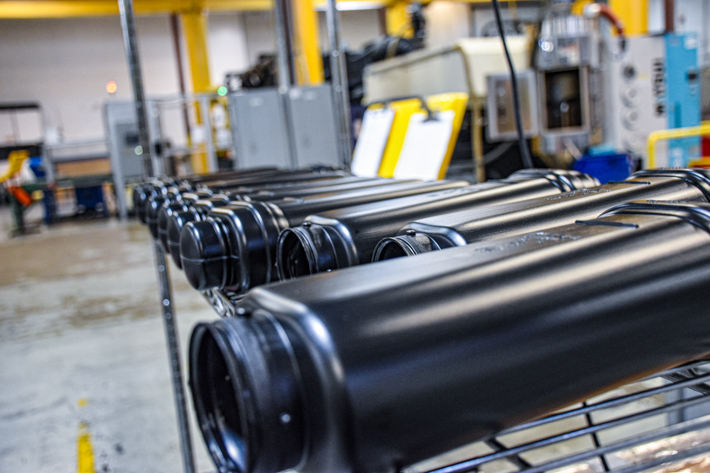
Weight Savings
Our process allows reduced material use while maintaining durability, ideal for industries where weight reduction matters.
Excellent Product Consistency
Delivers tight dimensional control and uniform wall thickness, ensuring reliable downstream compatibility with capping, labeling, and filling equipment.
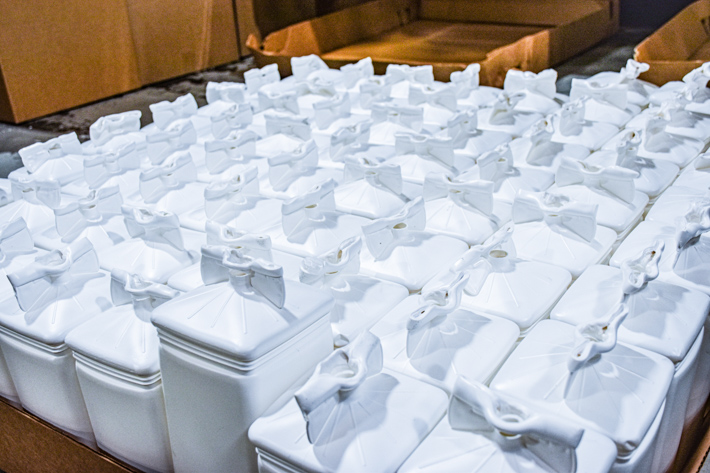
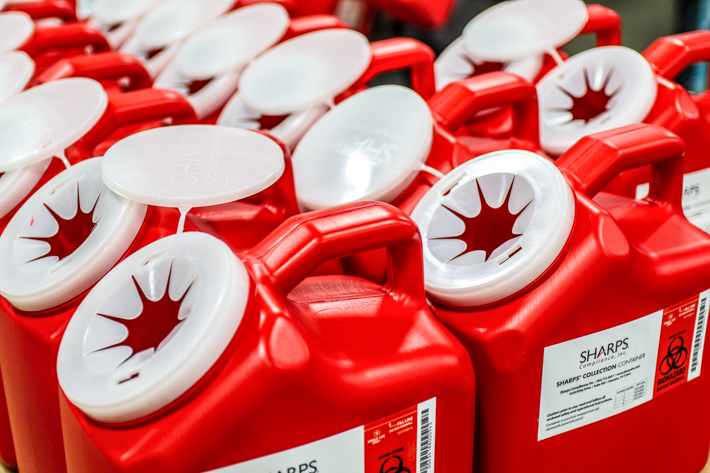
Enhanced Product Integrity
Results in strong, impact-resistant bottles that protect contents during storage, handling, and transport, even in demanding environments.
Sustainability and Environmental Friendliness
Enables thinner-walled bottles with less material, supports use of recyclable and recycled plastics, and helps customers meet sustainability goals.
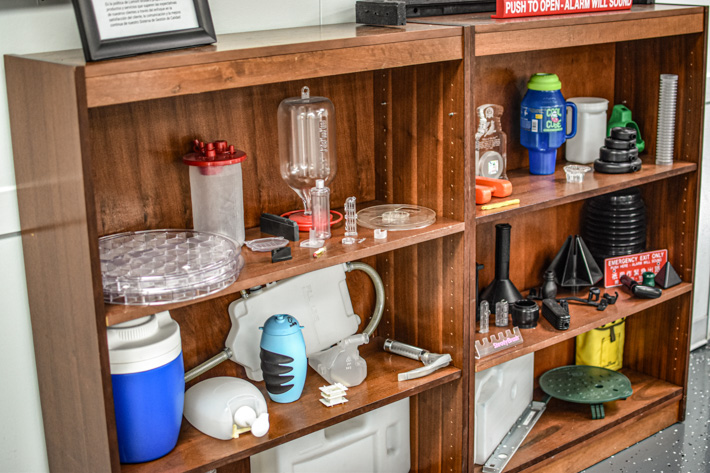
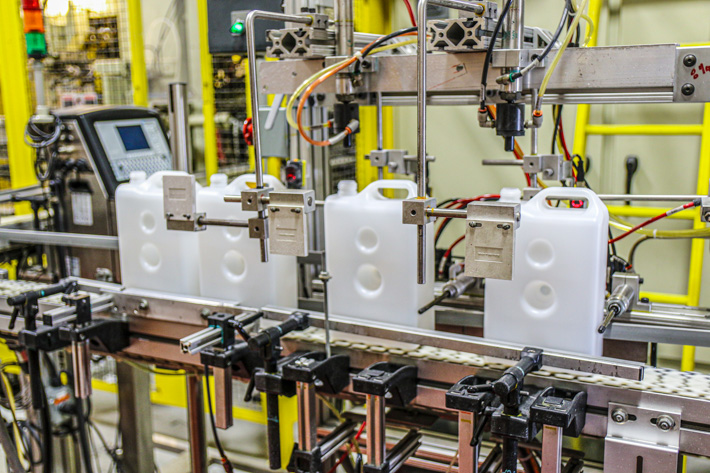
Strength & Durability
High-pressure injection creates dense, structurally sound parts that are resistant to wear for automotive, industrial, and consumer product use.